Trocken und staubig fängt es an.
In der Masseaufbereitung werden Kaolin, Feldspat, Quarz und Tone mit Wasser zu Schlicker verflüssigt und gründlich gemischt. Der dünnflüssige Tonschlicker muss garen und kann dann über Rohrleitungen durch den Betrieb gepumpt werden.
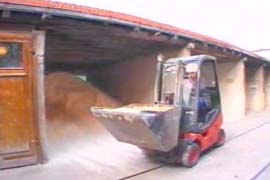
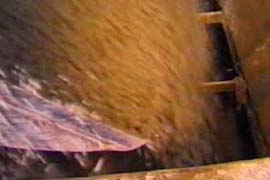
Masseaufbereitung
Im nächsten Schritt wird eine formbare Tonmasse gewonnen.
Mit Filterpressen wird dem flüssigen Tonschlicker Wasser entzogen. So entstehen Filterkuchen, die weiterverarbeitet werden können. Der Schlicker kann aber auch jetzt schon in Formen gefüllt werden, die für Giessware verwendet werden.
Filterpresse und Giesston
Die feuchten Filterkuchen werden in der Strangpresse wie in einem Fleischwolf vermahlen und gepresst. Dabei wird dem Ton Luft entzogen. Als Ergebnis stehen handliche Tonrollen zur weiteren Verarbeitung zur Verfügung. Die Tonrollen sind je nach dem nun folgenden Maschinenbedarf dick oder dünn, weich oder fest.
Strangpresse und fertige Tonhubel
Die Tonmasse wird geformt.
Die Tonhubel werden in Scheiben geschnitten und die Abschnitte fallen in Gipsformen. Mit dem rotierenden Metallrollerkopf wird der Ton in die Gipsformen gedrückt (eingedreht). An einer Tassentaktmaschine, mit der Tassen- und Becherkörper geformt werden, geschieht das fast vollautomatisch. Bei einem Teller wird der Tonklumpen mit Hilfe des Rollerkopfes auf die Form gedreht (übergedreht).
Rollerkopf über Becherform und Tonhubel auf Tellerformen
Der flüssige Schlicker wird zur festen Form.
Im Stapelguss werden Gipsformen mit füssigem Ton befüllt. Der Gips saugt die Feuchtigkeit aus der Gießmasse. So wird der dünnflüssige Schlicker zu plastischen Henkeln, Kaffeekannen oder Sparschweinen - zu Gegenständen, die nicht drehrund sind und nicht auf einer rotierenden Scheibe geformt werden können.
Stapelguss für Henkel und Ausformen eines Giessartikels
Formen, die nicht mit dem Rollerkopf gedreht werden können - Artikel wie Kannen oder Sparschweine - werden gegossen. Die Masse wird in Gipsformen gefüllt, einige Minuten stehen gelassen; es bildet sich die Wandstärke, der spätere Scherben. Überschüssige Giessmasse wird aus den Formen gegossen. Die Rohlinge werden aus ihren Formen genommen und kommen auf Trockenregale. Die Ränder der Formlinge werden anschliessend entgratet und sauber verschwammt.
Entgraten und Verschwammen
Der Becher bekommt einen Henkel
Verputzt und getrocknet wird der gegossene Henkel mit Tonschlicker an den gedrehten Becherkörper angarniert.
Henkel in Henkelformen und Angarnieren am Becher
Der Schrühbrand kommt vor dem Glasieren.
Um die Waren weiterverarbeiten zu können, muss nun ein erster Festigungsbrand bei 1100 Grad stattfinden. Der Brand wird in Tunnel- oder modernen Haubenöfen durchgeführt. Danach erst sind die Artikel hart und fest und können glasiert, gedruckt oder bemalt werden.
Ofengestelle und Tauchglasieren
Um den Waren eine glänzende Oberfläche zu geben, müssen sie glasiert werden. Glasur schwebt als fein gemahlenes Glas in einer wässrigen Lösung, in die alle Artikel getaucht werden müssen. Obwohl bereits gebrannt saugt der poröse Scherben die Glasur an. Anschließend müssen die Produkte noch einmal zum Glasurbrand (Glattbrand) bei 1200 Grad in den Ofen.
Dekore verschönern die Waren.
Schiebebilder werden mit Hilfe einer Trägerfolie auf den bereits glasierten und gebrannten Teller aufgelegt. Danach werden bei 850 Grad die Dekore eingebrannt; das ist der dritte Brand. Im Siebdruck lassen sich gerade Flächen auch schon vor dem Glattbrand bedrucken.
Dekorbild platzieren und Direktdruck
Bevor die fertig gebrannten Waren im Lager auf ihre Auslieferung warten können, werden sie auf Fehler untersucht. Kriterien zur Sortierung sind fabrikseitig festgelegte Eigenschaften und Erwartungen der Konsumenten.